MEGGLE Excipients: Cornerstones for reliable Continuous Manufacturing (CM) processes
MEGGLE Excipients has more than 70 years of experience in the field of pharmaceutical excipients. As experts in direct compression, wet and dry granulation, we can help you to select the right excipient for your next continuous manufacturing project.
Continuous manufacturing will play a significant role in the pharmaceutical industry over the coming years. Our extensive portfolio of CM-ready excipients combined with our expertise in production processes, regulatory affairs and packaging options will ensure the success of your CM project.
For an overview about continuous manufacturing in general and the role of excipients in particular, please check our presentation
“DC lactoses: Cornerstones for reliable continuous manufacturing processes” which is available in a PDF or video format.
You can expect the following content:
- What is continuous manufacturing?
- Advantages of continuous manufacturing
- Challenges in continuous manufacturing
- Important excipient requirements
- Performance of MEGGLE excipients in a continuous manufacturing setting for the production of Vitamine B2 tablets.
- Summary
If you are interested, you can request the presentation via the contact form.
Our experts are looking forward to your inquiry.
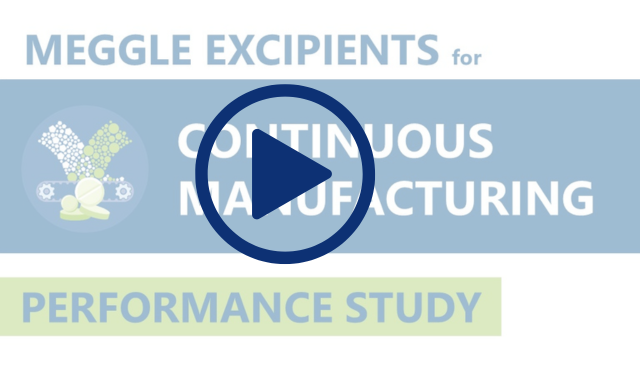
PRESENTATION REQUEST FORM
Continuous Manufacturing in the pharmaceutical industry – A promising solution.
Batch manufacturing is the proven and trusted process for manufacturing pharmaceutical products.
However, the interest of the industry to move to continuous manufacturing is increasing.
A key driver is the FDA, the U.S. Food and Drug Administration. The opinion of the FDA is, that continuous manufacturing has the possibility to improve product quality, reduces medicine shortages, and increases efficiency, among other benefits. Continuous manufacturing is supported by many regulatory bodies as it is consistent with the quality-by-design (QbD) approach for the development of pharmaceutical products.
Advantages of Continuous Manufacturing
In continuous manufacturing, a pharmaceutical product is produced without interruption. The entire process takes place on one production line, from start to finish, without stop.
Continuous Manufacturing (CM) in pharmaceutical production offers several advantages over traditional batch manufacturing. Here are the key benefits:
Increased Efficiency and Speed
CM allows for the continuous flow of materials through the production line, reducing production time and minimizing delays compared to batch processing, where production must stop and restart between each batch.
Improved Quality Control
CM incorporates real-time monitoring and automation, allowing for consistent product quality. Process analytical technology (PAT) can detect and correct deviations in real-time, reducing the risk of defects or out-of-specification products.
Reduced Costs
By eliminating downtime between batches, CM reduces operational costs, such as labor, equipment usage, and energy consumption. Additionally, less waste is generated due to improved control over the manufacturing process.
Scalability and Flexibility
CM enables faster scalability of production without the need for large-scale modifications. The same equipment can be adjusted to produce different product volumes or variations, offering flexibility in meeting market demands.
Minimized Inventory and Space Requirements
Continuous processes require less on-site storage of raw materials and finished products, reducing the need for large inventories and warehouse space.
Sustainability and Environmental Benefits
CM often consumes less energy and generates less waste, contributing to a more sustainable manufacturing approach.
Enhanced Regulatory Compliance
Regulatory agencies, such as the FDA, support CM due to its potential for enhancing product quality and manufacturing efficiency. Continuous monitoring helps meet stringent regulatory standards more effectively.
Overall, CM offers a streamlined, cost-effective, and high-quality method for pharmaceutical manufacturing that aligns with modern demands for faster production cycles and improved product consistency.