Reliable tableting
MEGGLE has it.
The right lactose product for tableting
It may seem that tableting should be the least concern when it comes to the production of solid oral dosage forms, but talking to production people, this supposedly simple process still holds a lot of surprises, not necessarily desired in the highly regulated pharmaceutical industry.
Part of the reason for unwanted surprises can be attributed to the lack of understanding and acknowledgement of tablets´ compaction complexity. Furthermore, there is only little incentive to go into detail, if it is more cost effective to deal with a marginal material loss rather than trying to overhaul an old formulation, which may have been around for decades. Nevertheless, from a scientific point of view, it is imperative to shed light onto the tablet compaction process. Luckily, the pharma regulations´ initiative to promote the concept of quality by design (QbD) will help the pharmaceutical industry in the long run to better understand material and process parameter, and in particular their interplay.
Excipients for tableting: Variety of products
The idea to break down the compaction process into critical material attributes (CMA) and critical process parameters (CPP) could be a first step, in order to get a deep understanding of what is really going on. Material attributes of raw materials, such as particle size distribution (PSD) and bulk density (BD) are common attributes, but they are not necessarily good predictors for a satisfying compaction later on. Therefore, one would spend more effort on developing an ultimate intermediate, which may be a granulate or a powder blend, which carefully crafted provides consistently excellent flowability and compactibility. If one decides to go with simple powder blends as intermediates, it may seem appropriate to choose an excipient based on the level of consistency (intra as well as inter lot-to-lot variability) it can provide, as there is no further production step, which can make up for the variability of the raw material.
Important: a close collaboration between the drug and excipient manufacturer
Although MEGGLE has readily available a wide range of products which fit the needs of the majority of customers, MEGGLE is committed to go the extra mile by providing tailor made products, which are developed in a highly cooperative manner with our customers. As MEGGLE is fully equipped with the technologies suitable for sieving, milling, agglomeration, and spray-drying a remarkable high degree of customization can be achieved. The customization, however, is not exclusively limited to our “lactose only” products. MEGGLE’s expertise in co-processing also allows for tailor-made co-processed products.
This clearly emphasizes the important role of an excipient manufacturer and distinguish the favorable from the unfavorable ones. If one decides for the need of a granulation step, a consistent raw material or at least a material, having consistent CMAs should be taken into consideration. The most straightforward approach should be a close collaboration between the drug and excipient manufacture. This should turn tableting into what it actually is – a simple process.
MEGGLE’s lactose grades suitable for tableting are available under the trade names GranuLac® 70, GranuLac® 80 GranuLac® 140, GranuLac® 200, GranuLac® 230, SorboLac® 400, Tablettose® 70, Tablettose® 80, Tablettose® 100, FlowLac® 90, FlowLac® 100, DuraLac® H, MicroceLac® 100, Cellactose® 80, StarLac®, RetaLac®, CombiLac®
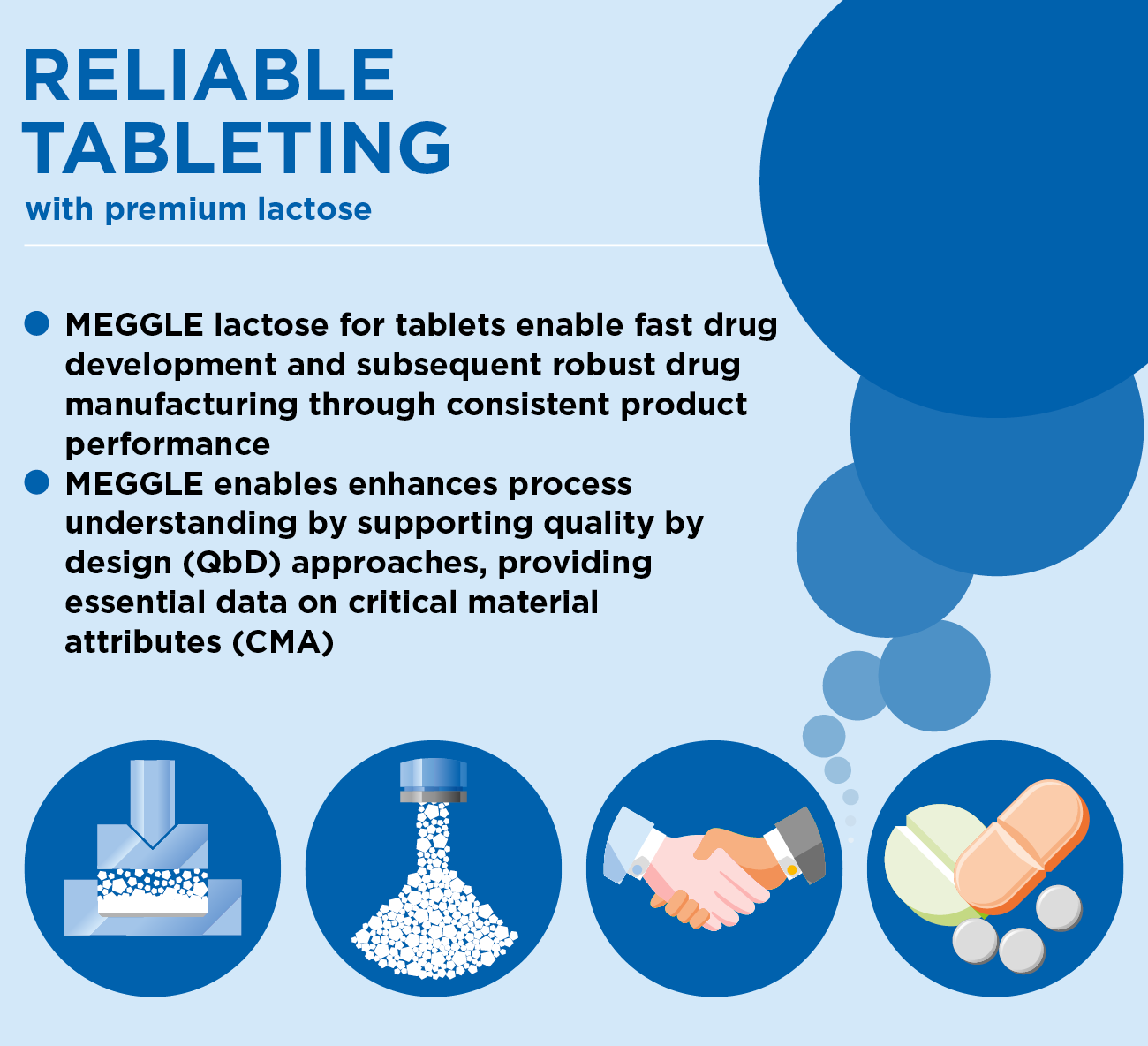
Information / Sample request:
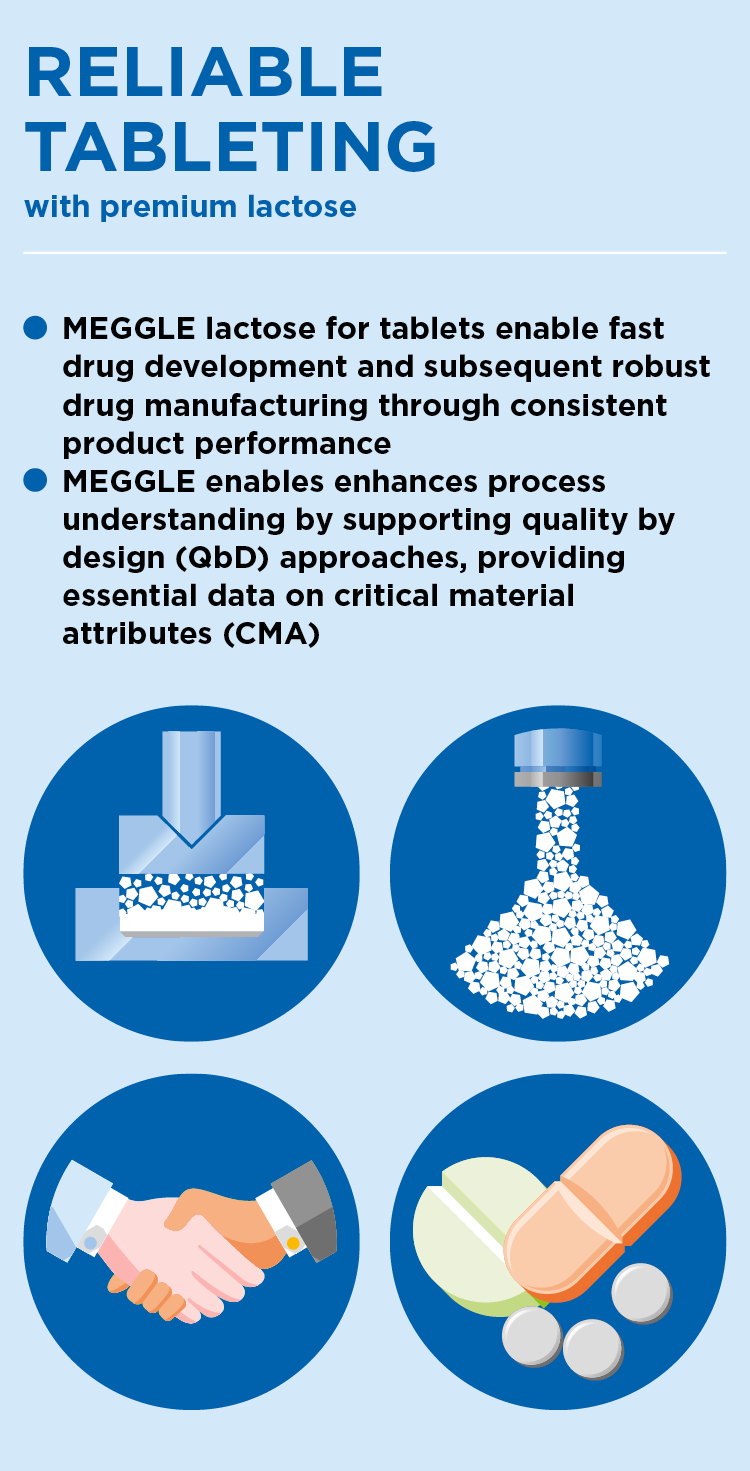
MEGGLE has it.
The right lactose product for tableting
It may seem that tableting should be the least concern when it comes to the production of solid oral dosage forms, but talking to production people, this supposedly simple process still holds a lot of surprises, not necessarily desired in the highly regulated pharmaceutical industry.
Part of the reason for unwanted surprises can be attributed to the lack of understanding and acknowledgement of tablets´ compaction complexity. Furthermore, there is only little incentive to go into detail, if it is more cost effective to deal with a marginal material loss rather than trying to overhaul an old formulation, which may have been around for decades. Nevertheless, from a scientific point of view, it is imperative to shed light onto the tablet compaction process. Luckily, the pharma regulations´ initiative to promote the concept of quality by design (QbD) will help the pharmaceutical industry in the long run to better understand material and process parameter, and in particular their interplay.
Excipients for tableting: Variety of products
The idea to break down the compaction process into critical material attributes (CMA) and critical process parameters (CPP) could be a first step, in order to get a deep understanding of what is really going on. Material attributes of raw materials, such as particle size distribution (PSD) and bulk density (BD) are common attributes, but they are not necessarily good predictors for a satisfying compaction later on. Therefore, one would spend more effort on developing an ultimate intermediate, which may be a granulate or a powder blend, which carefully crafted provides consistently excellent flowability and compactibility. If one decides to go with simple powder blends as intermediates, it may seem appropriate to choose an excipient based on the level of consistency (intra as well as inter lot-to-lot variability) it can provide, as there is no further production step, which can make up for the variability of the raw material.
Important: a close collaboration between the drug and excipient manufacturer
Although MEGGLE has readily available a wide range of products which fit the needs of the majority of customers, MEGGLE is committed to go the extra mile by providing tailor made products, which are developed in a highly cooperative manner with our customers. As MEGGLE is fully equipped with the technologies suitable for sieving, milling, agglomeration, and spray-drying a remarkable high degree of customization can be achieved. The customization, however, is not exclusively limited to our “lactose only” products. MEGGLE’s expertise in co-processing also allows for tailor-made co-processed products.
Packaging
This clearly emphasizes the important role of an excipient manufacturer and distinguish the favorable from the unfavorable ones. If one decides for the need of a granulation step, a consistent raw material or at least a material, having consistent CMAs should be taken into consideration. The most straightforward approach should be a close collaboration between the drug and excipient manufacture. This should turn tableting into what it actually is – a simple process.
MEGGLE’s lactose grades suitable for tableting are available under the trade names GranuLac® 70, GranuLac® 80 GranuLac® 140, GranuLac® 200, GranuLac® 230, SorboLac® 400, Tablettose® 70, Tablettose® 80, Tablettose® 100, FlowLac® 90, FlowLac® 100, DuraLac® H, MicroceLac® 100, Cellactose® 80, StarLac®, RetaLac®, CombiLac®
MEGGLE has it.
The right lactose product for tableting
It may seem that tableting should be the least concern when it comes to the production of solid oral dosage forms, but talking to production people, this supposedly simple process still holds a lot of surprises, not necessarily desired in the highly regulated pharmaceutical industry.
Part of the reason for unwanted surprises can be attributed to the lack of understanding and acknowledgement of tablets´ compaction complexity. Furthermore, there is only little incentive to go into detail, if it is more cost effective to deal with a marginal material loss rather than trying to overhaul an old formulation, which may have been around for decades. Nevertheless, from a scientific point of view, it is imperative to shed light onto the tablet compaction process. Luckily, the pharma regulations´ initiative to promote the concept of quality by design (QbD) will help the pharmaceutical industry in the long run to better understand material and process parameter, and in particular their interplay.
Excipients for tableting: Variety of products
The idea to break down the compaction process into critical material attributes (CMA) and critical process parameters (CPP) could be a first step, in order to get a deep understanding of what is really going on. Material attributes of raw materials, such as particle size distribution (PSD) and bulk density (BD) are common attributes, but they are not necessarily good predictors for a satisfying compaction later on. Therefore, one would spend more effort on developing an ultimate intermediate, which may be a granulate or a powder blend, which carefully crafted provides consistently excellent flowability and compactibility. If one decides to go with simple powder blends as intermediates, it may seem appropriate to choose an excipient based on the level of consistency (intra as well as inter lot-to-lot variability) it can provide, as there is no further production step, which can make up for the variability of the raw material.
Important: a close collaboration between the drug and excipient manufacturer
Although MEGGLE has readily available a wide range of products which fit the needs of the majority of customers, MEGGLE is committed to go the extra mile by providing tailor made products, which are developed in a highly cooperative manner with our customers. As MEGGLE is fully equipped with the technologies suitable for sieving, milling, agglomeration, and spray-drying a remarkable high degree of customization can be achieved. The customization, however, is not exclusively limited to our “lactose only” products. MEGGLE’s expertise in co-processing also allows for tailor-made co-processed products.
Packaging
This clearly emphasizes the important role of an excipient manufacturer and distinguish the favorable from the unfavorable ones. If one decides for the need of a granulation step, a consistent raw material or at least a material, having consistent CMAs should be taken into consideration. The most straightforward approach should be a close collaboration between the drug and excipient manufacture. This should turn tableting into what it actually is – a simple process.
MEGGLE’s lactose grades suitable for tableting are available under the trade names GranuLac® 70, GranuLac® 80 GranuLac® 140, GranuLac® 200, GranuLac® 230, SorboLac® 400, Tablettose® 70, Tablettose® 80, Tablettose® 100, FlowLac® 90, FlowLac® 100, DuraLac® H, MicroceLac® 100, Cellactose® 80, StarLac®, RetaLac®, CombiLac®